|
Final Repot: The final report analyses revolve around the project's driving schedule. Areas of analysis include change order management, the implementation of precast panels, use of virtual mock-ups for short interval production scheduling, and investigating the use of partial modularization versus floor-to-ceiling modules. The Final Report can be accessed by clicking the image directly to the rigth. The Executive Summary can be seen and accessed directly below the Final Report.
Analysis 1: Change Order Management
Change order management was chosen for research because of the extensive volume and costs associated with changes, accounting for nearly a 40% increase in the original contract value. A process map was created and durations of specific change orders were investigated to determine where issues and bottlenecks were developing in this process. A significant amount of time was spent by management dealing with changes and productivity was hindered as the volume continued to accumulate throughout construction. This research has led to three key recommendations. It is suggested to give the construction manager the authority to approve small-scale changes as that potentially has the largest impact, the owner should consider purchasing preconstruction services, and finally to transition to an alternative change review process.
Analysis 2: Implementation of Precast Panels
With schedule being the driving factor, implementing precast panels was considered as challenges arose hindering progress and delaying the project schedule. A complete analysis of the building façade was performed and showed that the mechanical system will not be affected as long as proper measures are taken to prevent thermal bridging while the structural steel will not need to be upgraded for the additional loading. Precast panels will have a much higher unit cost than using brick due to the irregularity of the façade and limited amount of repetition allowed by the current design, but the schedule savings would be the largest benefit for the project. With the watertight milestone advancing two months, major interior finishes work and construction of the elevator could begin much sooner. The estimated $125,371.56 savings make use of precast panels a logical alternative.
Analysis 3: Use of Virtual Mock-ups and Implementation to SIPS
Constructability issues at building connections led to the study of implementing virtual mock-ups. The Tyson’s Corner case study revealed benefits for the owner but little use for those in the field while more changes were created requiring additional costs. This analysis focused more on ways to benefit field personnel and increase efficiency. Because of this, a Short Interval Production Schedule (SIPS) was created as a potential opportunity to save labor time and using a mock-up could help reach the level of detail needed. Use of the single mock-up analyzed can produce over $1,700 worth of possible savings. Savings are expected to be greater if the same measures were taken for other areas of the building. It is recommended to use virtual mock-ups for building interface and tie-ins, and implement the use of SIPS. Although these activities did not affect the critical path, time savings can help offset the cost of additional upfront coordination.
Analysis 4: Complete Headwall Modularization vs. Partial Modularization
The final analysis was intended to further increase productivity and decrease the overall project schedule. Modular headwalls were used; however, productivity was still an issue as in-wall rough-ins were very labor intensive. Full-size wall assembly modules would have been an ideal opportunity for increasing labor productivity and better streamlining the MEP rough-in sequence. Also, changes had such a large impact on rough-ins that resulted in significant delays. Floor-to-ceiling modules were proposed to eliminate any productivity issues. Utilizing the proposed system could have better eliminated a total of 563 man-hours, but a 0.49% increase to the original contract was estimated due to the high unit cost. If changes did not set back MEP rough-ins enough to prevent any critical path savings associated with the proposed system, reduced general conditions costs could further offset the higher unit cost. Although it appears that costs could not be justified in this case; it is recommended to incorporate more modularization in future projects because of the better opportunity to provide schedule savings and reduce the amount of labor needed, especially for systems that are the same from facility to facility.
|
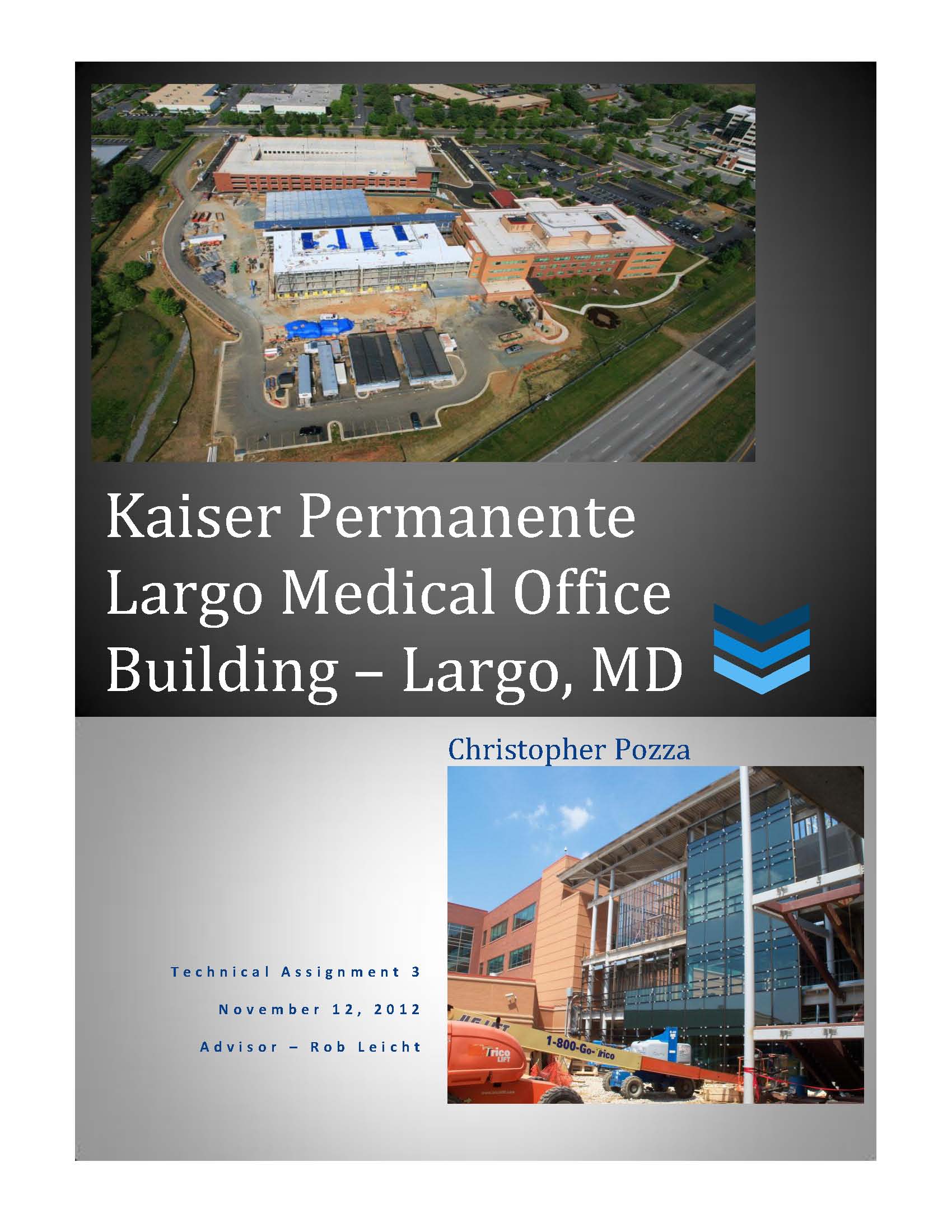
Final Report
Posted April 3, 2013
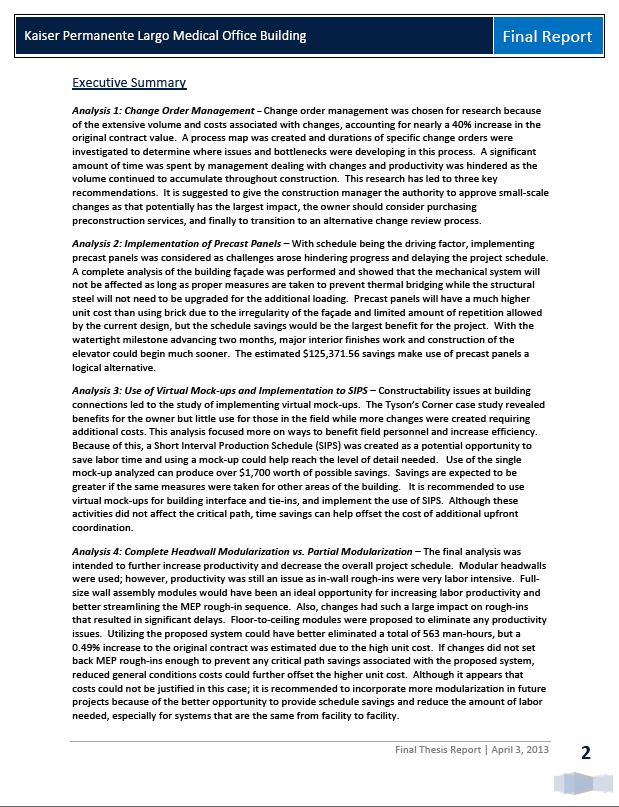
Executive Summary
Posted April 3, 2013
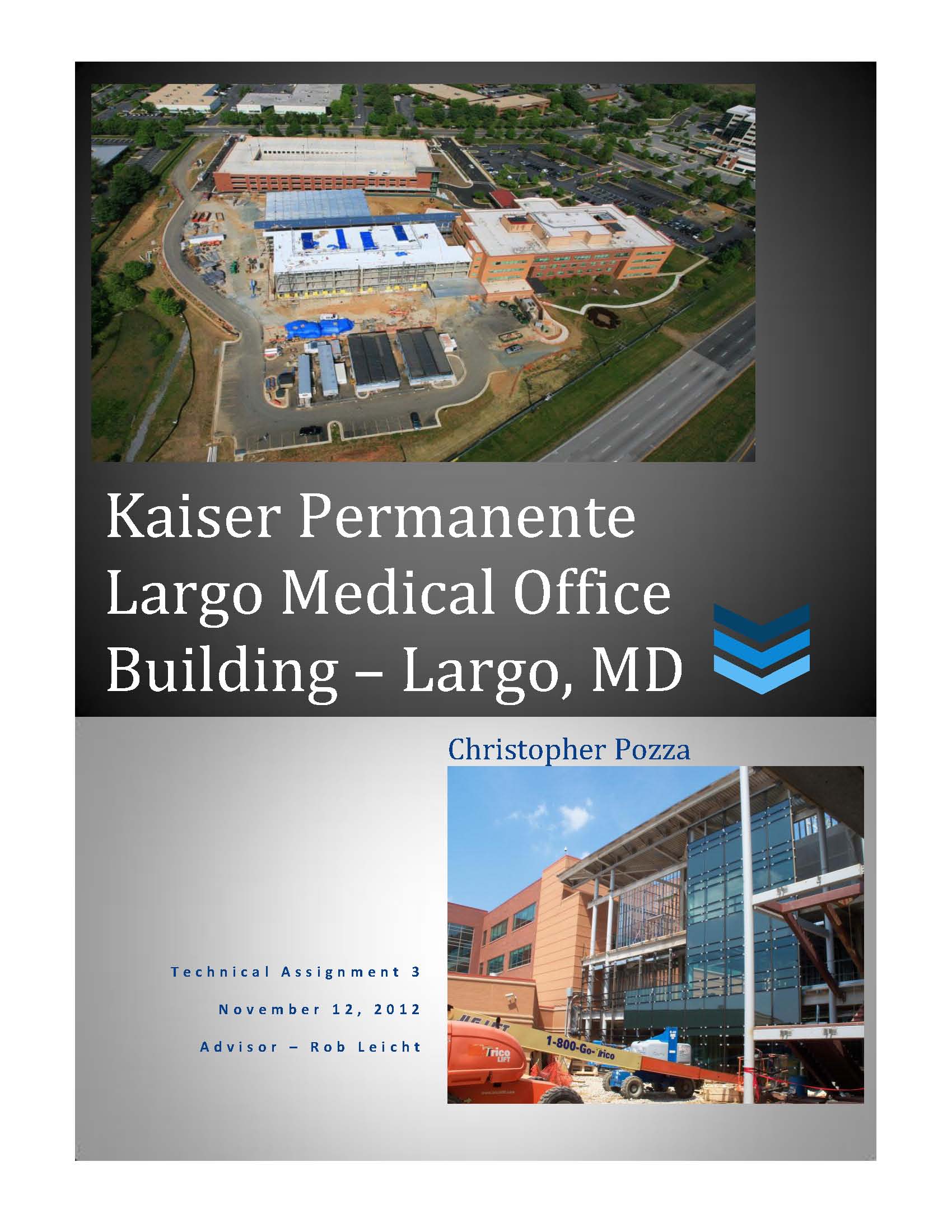
Report Only
Posted April 3, 2013
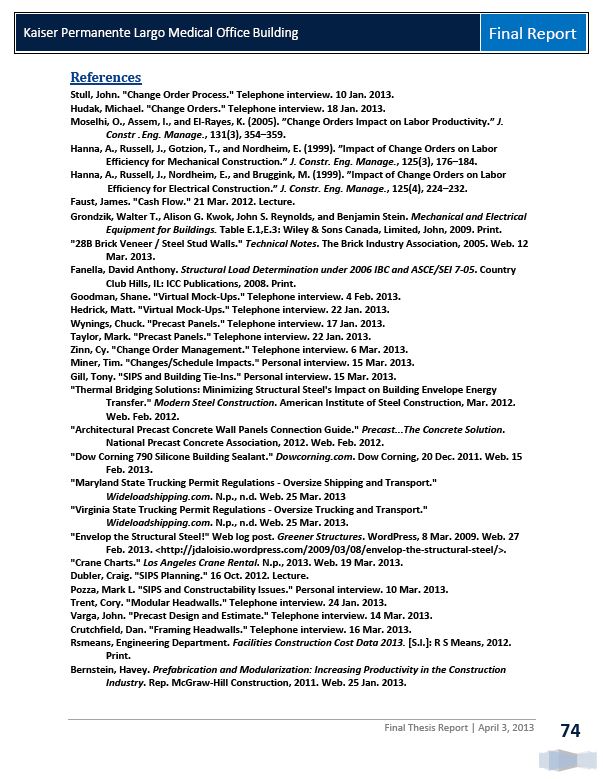
Appendices Only
Posted April 3, 2013 |